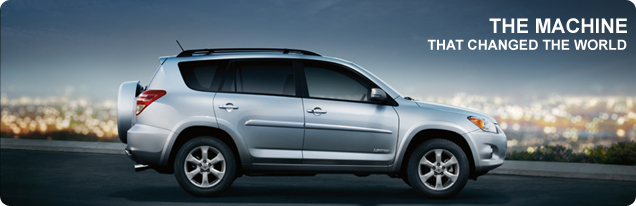
By Oskar Olofsson
TPM is a manufacturing-led initiative that creates a collaborative approach among all stakeholders within an organization¡ªparticularly between operations and maintenance¡ªin an effort to achieve production efficiency, uninterrupted operations and ensure a quick, proactive maintenance response to prevent equipment-specific problems.
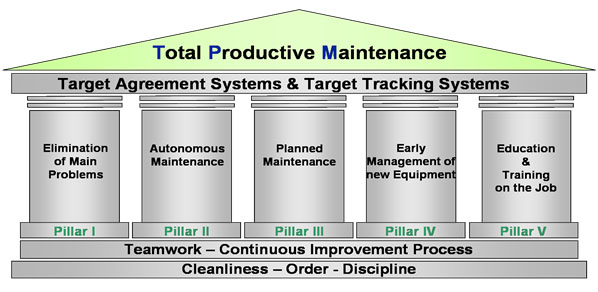
Fig 1. The 5 pillars of TPM
The goal of TPM is to create a production environment free from mechanical breakdowns and technical disturbances by involving everybody in maintenance duties without heavily relying on mechanics or engineers.
Modernization and the ongoing automation in different industries have noticeably amplified the gap between operators and their machines.
Years ago, machine operators were limited to manning their respective posts. Whenever there is a mechanical trouble, operators would stop working and would call in the mechanics to fix the problem. Even with the slightest snag, operators would leave everything to maintenance for fear of making the problem worse, and besides they don¡¯t want to take on the mechanics¡¯ jobs.
On the other hand, the traditional mechanics could love the smell of a breakdown. They know that they have become indispensable specialists in the trade¡ªthey are assured of a stable job every time a fix is needed. So, the vicious cycle goes on and on, and the aftermath of which is immense amount of waste: man hours, production time, opportunity lost, and ballooning maintenance expense.
But with the adoption and adaptation of Total Productive Maintenance, the vicious cycle has come to an end. Today, TPM builds on the classical Japanese concepts of autonomous maintenance with process mapping for cross-functional duties.
Coupled with the right tools and training, TPM equips the operators the necessary skills to address mechanical or equipment-related issues. Calling the engineers and mechanics is no longer necessary since operators are already prepared and confident in dealing with the problems.
Undoubtedly, Total Productive Maintenance is one of the most effective ways to create a lean organization with reduced cycle time and improved operational efficiency.
Lean Maintenance/TPM Assessment
Is your plant maintenance efficient and total productive?
How well do these Maintenance audit statements correspond to your facility?
1. The need for preventive maintenance is determined for every machine.
2. The production personnel are responsible for most of the maintenance inspections on their machines.
3. Production personnel are trained for maintenance work, and easy-to-understand instructions are readily available for every operator on duty.
4. What is to be done, who is responsible, and when it was last time it was checked/repaired is clearly communicated to everybody.
5. Production personnel are well trained in trouble shooting and maintenance jobs. They can describe malfunctions clearly and offer help during heavy repair works.
6. What ratio of all maintenance work is planned in advance?
7. "As our machinery is reliable, our maintenance personnel need to work during dayshifts only."
8. All maintenance works are registered in a computerized maintenance management system (CMMS)
9. We use reports from the computerized maintenance management system (CMMS) to make decisions.
10. We are using a mathematical model or computer aid to determine the right level of spare part inventory.
11. The maintenance department uses most of its time to improve the equipment, advanced inspections, and train the production personnel. Breakdowns are rare.
12. All levels of management are committed to maintenance issues and regular audits are carried out.
» More Information